Why the Differences DO Matter
It's safe to say that most of us are familiar with the proverbial saying "Rome wasn't built in a day." This saying is applied in many facets of life when describing that all great achievements take time and should not be rushed. We believe that the same is true for industrial-quality garage floor coating systems!
So, when comparing a traditional Two-Day garage floor installation to the glut of newly marketed, One-Day garage floor systems -- is faster really better?
In order to answer that question, we need to analyze the differences between those two processes. One-Day and Two-Day systems use different products and application techniques, while offering an end result that might look similar, but can definitely vary from a quality and durability perspective. Most importantly, it begs the question: Do One-Day applications provide the most benefit to the customer or to the contractors installing them?
PROCESS COMPONENTS
Before exploring the differences in types of product used, let's begin with the basics components of any professionally installed polymer- or resin-based flooring system: Substrate Preparation, Coating Materials, and Installation Expertise.
Substrate Preparation: The first component of the process is the preparation of the concrete substrate, which includes abrading the surface to Concrete Surface Profile CSP2, CSP3 or CSP4 by using industrial diamond-grinding equipment. Grinders are large machines that have rotating heads with diamond tooling attached and are obviously designed to grind the concrete. The goal of the diamond-grinding process is to remove existing contaminants (previous coatings, oil, dirt, road grime, etc.) and laitance, which "opens up" the pores of the concrete to create a profile that allows the material applied to create a strong mechanical and chemical bond with the concrete (see images below).
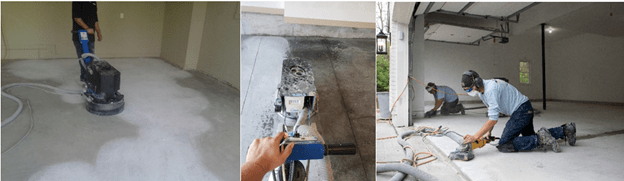
The substrate preparation process includes the restoration of any concrete imperfections, such as fissures, cracks, heaves, or spalling. To install a long-lasting coating system on any garage floor, it is imperative to restore the integrity of the substrate. Concrete repairs can vary from moderate to extreme, and there are several types of polymer-based products used to repair concrete, based on the severity of the damage.
Materials:
The second key component is the use of industrial-grade materials. These are much different materials than the products often purchased in kits at home improvement and paint stores. "Epoxies" or "Polymers" bought at retail stores are normally water-based or low-solids-content products, making them more DIY-friendly. Industrial coatings include epoxies, polyaspartics, polyureas, and urethanes. All include both a resin (Part A) and activator (Part B) component, hence the name "two-part." They are mixed together to initiate an exothermic, chemical reaction with the prepared substrate.
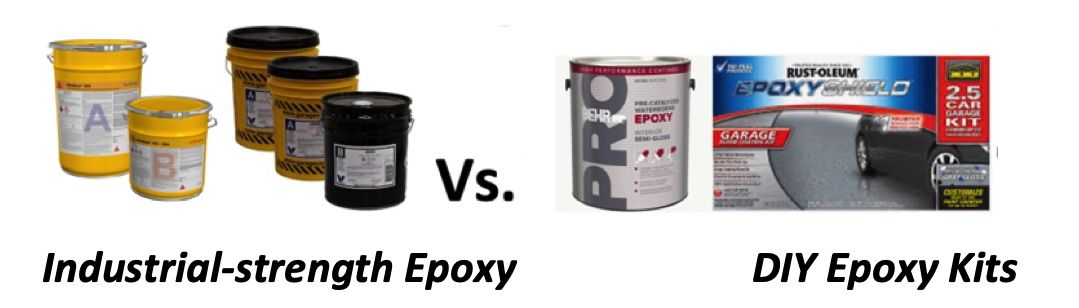
Installation Expertise:
Finally, the most important (and often the most overlooked) aspect of a professionally-installed coating system is the experience of well-trained installation teams. These professionals are prepared to overcome the various challenges that often arise during the preparation and installation process. In addition, they must consider the Moisture Vapor Emissions Rate (MVER) of each substrate, as it relates to the substrate temperature, pH levels, and other external variables such as the ambient temperature, relative humidity, and dew point.
SYSTEM COMPONENTS
The most common type of garage floor coating system on the market today is known by coating professionals as a full-broadcast system. The materials are applied at prescribed coverage rates, based on manufacturer guidelines and the installation company's techniques, to achieve a stated finish quality and specific-mil thickness.
The components of a full-broadcast system are:
- Base coat - the material that should bond with the concrete to receive the broadcasted medium.
- Broadcast medium - an intermediate layer of polymer flakes (chips) or decorative quartz, sand, etc.
- Top coat or clear coat - The layer that protects the broadcast medium and overall coating system.
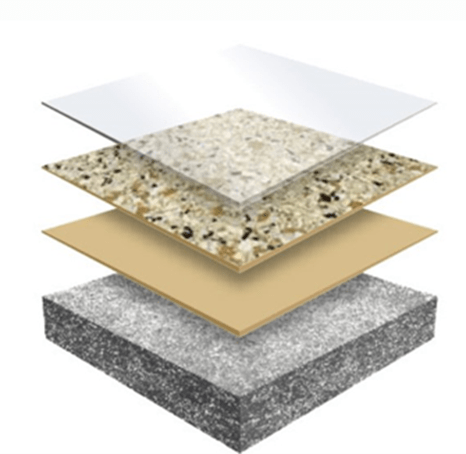
When assessing the quality, durability, and longevity of coating systems - the type of the material used, the quantity of the material actually applied, and the installation methodology are crucial to long-term viability. All of these variables are dictated by an internal objective of the installation company.
For end users to achieve their goals (easy cleaning, durability, longevity, cosmetics, slip-resistance, et al), no single facet of a coating system is as important as the base coat. It is the layer that connects the entire coating to the concrete and determines its durability and longevity through permanent adhesion.
PRODUCT COMPONENTS
The following will detail the specifics of the products that are used on all facets of both One- and Two-Day coating systems - but with specific focus on the all-important base coat.
Both installation methods utilize Polyaspartic top coats, which is a best-in-class product that provides the broadest level of chemical protection, abrasion resistance and uV stability. It is widely used in both industrial and residential installations and will be explained in more detail below. The significant difference in the two methodologies comes down to which product is used as the base coat for bonding to the concrete. Two-Day systems typically use a high-solids or 100% solids, Industrial-Strength Epoxy for the base coat, whereas One-Day systems typically use a Polyurea material for the base coat. Let's explore the details of each below.
Epoxies:
Epoxies were commercialized in the 1950s and are resin-based polymers utilized for their unmatched adhesion strength and durability. These attributes are achieved via epoxy's inherent chemistry, which makes it cure slower and penetrate further into concrete substrates, creating a superior bond for the coating system as a whole.
Epoxy can be applied at a much thicker mil rate than other polymers (from 15 to 50 mils). The added thickness improves the appearance and structural integrity of older concrete floors, which can often be wavy and in disrepair, and also provides increased durability, strength, and impact resistance. Epoxy also has a significantly greater tolerance for being applied to concrete that has higher moisture levels.
Industrial-strength epoxy (not the product sold in kits at retail stores) is the industry standard and is used by the majority of industrial and commercial coatings companies. These companies install polymer concrete coatings in the most demanding locations, including large factories, distribution centers, warehouses, and airplane hangars. They have become so well known, that many use the term "epoxy" as a universal term for any type of polymer coating.
Advantages of Epoxy Coatings:
- Slow curing time / longer Pot Life (allows for deeper penetration into substrate)
- Exceptional substrate adhesion (ASTM-7234 Pull Off Adhesion Strength)
- Exceptionally strong impact resistance - 10,000+ PSI pushing on surface (Compressive Strength)
- Higher tolerance to permanently bond to wet concrete with high MVER (Moisture Vapor Emissions) from 3 lbs. to 20 lbs.
Disadvantages of Epoxy Coatings:
- Require extensive surface abrasion (CSP2 or CSP3) to allow for 3-6 mils of penetration into substrate
- Longer back-to-service time
- Less chemical resistance than other polymers
- Lower uV Resistance - May amber, fade, or yellow over time
Polyureas:
Polyureas are considered the new kids on the block when it comes to polymer coatings. However, they have been around for more than 20 years. Because of their chemical resistance, polyureas were initially developed for corrosion protection in metal pipelines, water towers, and liquid storage tanks. Historically, they have been applied through specialized spray guns, due to their thinner viscosity and extremely fast (almost immediate) curing times. This makes polyureas ideal for coating vertical and rounded surfaces.
Over the years, large chemical companies have reformulated polyureas to allow for easier use by extending their working times, which has enabled them to be used in other industries, such as concrete flooring. Eventually, using a molecular alteration, manufacturers recently created a different type of polyurea known as polyaspartic.
Both products, regardless of the nomenclature, have nearly identical attributes, including fast curing and exceptional elongation rates. Polyaspartics generally contain higher solid content than polyureas and, as previously mentioned, are widely accepted as the premier, protective top coat in many industrial coating systems (because of their increased chemical-resistance, abrasion resistance and uV stability).
Additionally, polyureas have an extremely low tolerance for any moisture (as you might recall their roots were designed for applying to metal - not concrete). This can make polyureas more vulnerable to delamination or adhesion failures when applied to concrete, when compared to industrial-strength epoxy.
Advantages of Polyurea (Polyaspartic) Coatings:
- Chemical resistance superior to other polymers
- uV Stable - less likely to amber, stain, or discolor
- Shorter back-to-service time
- Excellent abrasion resistance and flexibility
Disadvantages of Polyurea (Polyaspartic) Coatings:
- Fast curing time (allows for minimal penetration into the substrate)
- Vulnerable to delamination & low tolerance for any substrate moisture if utilizing as base coat
- Must be applied thin, not allowing for maximum system build when broadcasting a flake into it
- Generally higher VOCs and odor due to containing more solvents than industrial-strength epoxies
One-Day vs. Two-Day System Claims:
Anyone considering a full broadcast system for their garage floor will likely encounter many claims regarding all the aforementioned products. Below, we summarize and clarify many of those claims to assist you in making an educated decision, based on factual and accurate information.
Claim: Industrial Epoxy is older technology. Reality: TRUE
Industrial epoxy is indeed an older coatings technology, making it tried and true. Though they may appear to be casual environments, residential garages are some of the most abusive environments around and require coatings that can withstand the weight of vehicles and resist delamination from contact with hot tires, which can reach temperatures as low as 30 degrees in the winter and over 150 degrees in the summer.
Industrial-strength epoxy, while older than some of the other polymers, remains the preferred product to connect a coating system directly to concrete. Industrial epoxy's ability to cure slowly and wick into the prepared concrete surface allows it to integrate into the concrete (3-6 mils) and create a tenacious and permanent bond.
Quicker-curing polyurea base coats are renowned for not bonding as well to bare concrete and also lacking moisture tolerance, both of which could make them susceptible to delamination over time. Regardless of the recent technology improvements made with polyureas, the time-tested effectiveness of utilizing high-solids, industrial epoxies as the base coat are proven and trusted by the coatings industry. This is why industrial epoxies continue to be the product of choice by coating manufacturers, industrial-coating supply houses, and commercial coating contractors alike.
The bottom line is that there is no one-size-fits-all approach to coatings. So, when selecting the correct coating system for a specific application, the decision should be driven by which products will deliver the highest-quality system to the consumer and not what is easiest or fastest for the installation company.
Claim: Epoxy is inferior to Polyurea. Reality: Both TRUE and FALSE
There are undisputed attributes of polyaspartics and polyureas that are superior to industrial epoxies, as discussed above. Some of these attributes include abrasion resistance, chemical resistance, uV resistance, and back-to-service times.
However, none of these polyurea benefits pertain to what remains the lowest-common-denominator in coating systems: The durability and longevity achieved through permanent adhesion to the concrete. Without a permanent bond, all of the other ancillary benefits of the garage floor coating system are negated.
Polyureas were not originally engineered for bonding strength to concrete. They were developed to be applied at a thin mil to achieve a quick bond to non-porous metals, with a focus on their superior chemical resistance and uV stability. More recently, One-Day installers have touted polyurea's greater elasticity. While this may be true when laboratory tested independent of other products, most manufacturers agree that a polyurea having greater flexibility is more of marketing point and not an important product characteristic when coating concrete in a residential garage.
In contrast, industrial epoxies have been proven for decades to be the best polymer for bonding directly to concrete and remains as the best option for experienced, commercial coatings installation companies to use as the base coat in garage-floor coating systems.
The reality is that systems using a polyurea base coat are easier and less time-consuming to install, as they only require one day for installation. One-Day garage floor companies often state that they provide warranties ranging from 15 years up to limited lifetime warranties. How are such warranty and longevity claims substantiated, when the products used for One-Day garage floor coating systems are new to the market and untested for such extensive longevity claims?
Claim: One-Day Installations using polyurea base coats are "Stronger Than Epoxy" Reality: FALSE
Countless companies that install One-Day garage floor systems publish claims that their systems using polyurea base coats are up to 20 times stronger than systems using epoxy base coats, while presenting no factual data to support their statements. These claims are misleading, as there are many variables in play when comparing the strength of any polymer's bond to concrete.
Which type of epoxy do those claims refer to -- industrial-strength epoxy, which is widely used in factories, airplane hangars, and warehouses, or DIY epoxy kits purchased at local home-improvement or paint stores? Epoxies in DIY kits, which may be water- or solvent-based, often have lower solids content than industrial-strength epoxies, resulting in a limited mechanical and chemical bond with the concrete. This makes them more user friendly for homeowners or house painters who install the products themselves, but it reduces their durability and longevity. These inferior attributes of DIY epoxy kits can lead to delamination, coatings failures, and costly reinstallations in the future.
So, applying a blanket statement that any polyurea is "stronger" than epoxy is not true and would require facts to support such a claim. It's not an apples-to-apples comparison. The strength of any polymer is measured in several areas: Bond Strength, Compressive Strength, Flexural Strength, and Tensile Strength.
The Bonding Strength, which is the measurement of how well a polymer bonds to the substrate, is considered the most important "strength" attribute. No other strength-related traits have any merit if the coating's bond to the substrate is not permanent. For example, if the bond strength of the polymer is greater than the tensile strength of concrete itself, then the strength limitations will cause the concrete to fail prior to any polymer failing, be it polyurea or epoxy. This is measured by the ASTM D-7234 test, which is the Standard Test Method for Pull-Off Adhesion Strength of Coatings using an Elcometer as demonstrated below.
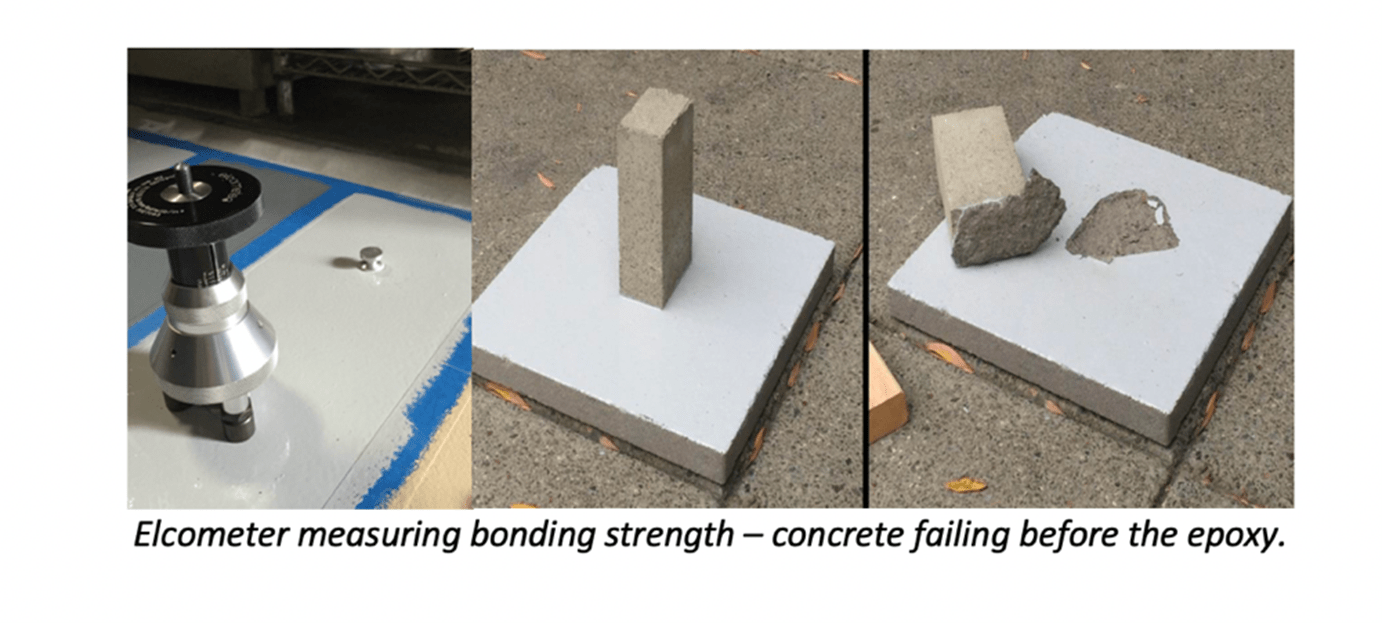
Claim: Polyurea systems are similar in thickness to Industrial Epoxy/Polyaspartic Systems. Reality: FALSE
Many of the One-Day garage floor companies state that their total system build is equal to that of the Two-Day garage floor systems, and others conveniently omit this system characteristic. The thickness of a garage floor coating system is extremely important. If a coating is too thin, it will not provide sufficient protection during the day-to-day rigors of garage use. In contrast, if a coating is too thick, it will become too brittle. So, utilizing the correct product at the correct thickness in each stage of the process is vitally important for durability and longevity.
Polyureas can be prone to outgassing if applied too thick and are normally installed at 250-375 square feet per gallon (4-6 mils per coat). This creates an extremely thin base coat, in comparison to industrial epoxy base coats that are typically applied at 100-160 square feet per gallon (10-16 mils). Potential issues of a base coat being too thin are:
- Inconsistent coverage: Without enough base coat material to receive the broadcast medium (flakes), the base coat may be visible following the application.
- Reduced impact resistance: If less broadcast medium adheres to the base coat, it results in less of the protective top-coat material being applied to encapsulate the flakes.
- Less long-term durability: Using thinner polyurea base coats can lead to the overall system thickness being up to 50% less than a hybrid system utilizing an industrial epoxy base coat.
Higher Compressive Strength, Tensile Strength, and Elongation numbers alone do not translate to a better-quality system. Professional companies must understand the solids content and spread rates for each product and how it translates to the coating's final DFT (Dry Film Thickness). Consequently, they use mathematical formulas to determine how much product needs to be applied per square foot, given the type of material used. This specific calculation allows for an accurate coating thickness and a predictable long-term performance.
Claim: Back-to-service time is shorter with a Polyurea system. Reality: TRUE
One-Day systems that use a polyurea base coat may allow for a full return to service within 24 hours, due to their faster curing times and thinner application. Two-Day systems using a hybrid approach allow for a next-day return to limited service (foot traffic & personal items), with vehicles allowed a few days later.
For this reason, One-Day systems can be the right option in settings that require as little downtime as possible (retail/commercial businesses) and that have little or no vehicular traffic. So, if being displaced from your residential garage for only one day is a higher priority than the longevity and durability offered by a hybrid, Two-Day coating system (using an industrial epoxy base coat and polyaspartic top coat), then a One-Day installation might be a good fit for your needs. This begs the question: if One-Day systems were actually better overall concrete coatings products, why would most industrial coatings contractors not use them as their standard base coat application?
Claim: Epoxy has seasonal limitations and cannot be installed in extreme cold or heat. Reality: FALSE
One-Day garage floor companies tout that their products can be installed in extreme temperature conditions. While this may be true, it is not relative to semi-exterior industrial epoxy installations, particularly on garage floors.
It is common sense that there is a significant difference between the temperature of the concrete substrate and the ambient temperature. The main focus during a quality coating installation is the temperature of the concrete itself. Since garages aren't typically directly exposed to the elements, the concrete temperature in garages stays relatively constant (between 35-75 degrees) throughout all seasons in most parts of the country.
These temperatures are well within the installation parameters of industrial epoxy. Additionally, all polymer coatings manufacturers offer cold- or warm-weather hardeners, to allow contractors to adjust the speed of the curing process, without jeopardizing the quality of the bond between the resin and concrete.
Final Thoughts:
Science and chemistry suggest that using the best attributes of each specific product within a coating system will deliver the best overall results for the customer. Industrial-strength epoxy is a better, all-around product for the base coat within a full-broadcast garage floor system, due to its proven ability to form a permanent mechanical AND chemical bond directly to a concrete substrate.
Likewise, the attributes of polyaspartics are better suited to be applied as a top coat, in order to utilize their abrasion, chemical, and uV resistance as the system's protective coat.
Sika USA is a global specialty chemical company and leader in the development and production of industrial-coating systems. Kelly Otts is their Senior Sales Representative for the Polymer Flooring and Wall Division and has 25 years of coatings experience. He states:
"Using a hybrid system of industrial-strength epoxy as a base coat and polyaspartic as a top or clear coat is the preferred industrial methodology for installing a full-broadcast flake system, these systems provide the best characteristics of both industrial-strength epoxy and polyaspartic, providing a best-in-class system that is durable, chemical resistant, abrasion resistant and uV stable and is why they have been the favored system of industrial, commercial, and residential contractors for decades."
Like countless other industrial and commercial coatings contractors with decades of proven results, we at Granite Garage Floors believe in providing the best overall product for our customers. Therefore, we utilize a hybrid coating system with a thicker, industrial-strength epoxy base coat and a polyaspartic top coat, leveraging the best-in-class attributes of each product to provide the highest-quality coating solution to our customers.
Intentionally investing in a more difficult and longer installation process to achieve a better end result is paramount to quality and longevity. The phrase, "Rome was not built in one day" is the epitome of a short-term sacrifice for a longer-term gain and lives on yet today, with respect to the time and effort required to install a permanent garage floor coating system...
Since 2009, Granite Garage Floors has successfully installed 10+ million square feet of residential garages and commercial coatings throughout the U.S. using the hybrid-system approach summarized above. These systems are professionally installed and backed by the best warranty in the industry -- a Lifetime Satisfaction Warranty and 100% Guarantee against hot-tire pick up, that is complemented by a best-in-class home-service experience.